How to Make a Coat
- Rory Duffy - Master Tailor
- Feb 23, 2021
- 5 min read
Updated: Mar 2, 2021
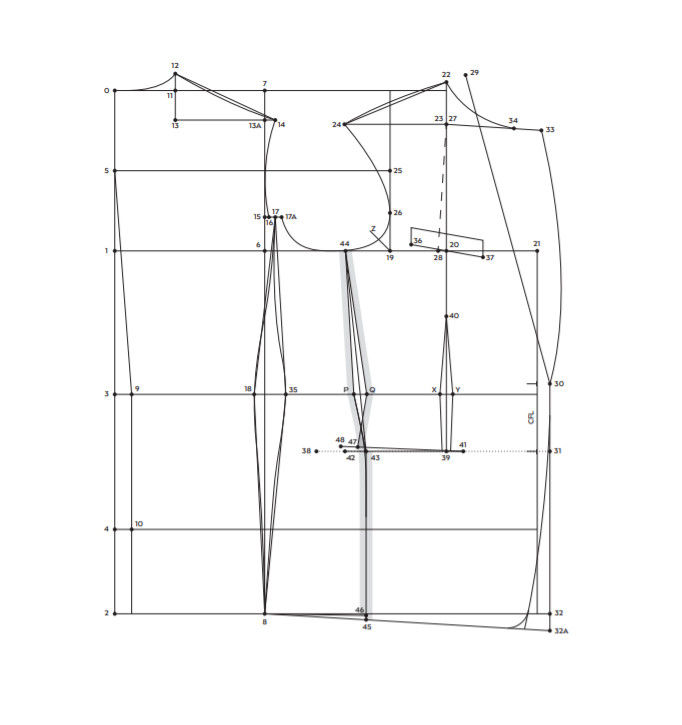
Video series available at https://vimeo.com/ondemand/thehta
Since the release of my free video series The Making of a Coat in 2012, I realised the need for a ’how-to’ video series on coat making and an in-house coat making class, particularly Savile Row coat making.
So many people say, ‘tailoring is a dying art’. It's not because there are fewer people taking up the needle but rather aspiring tailors are finding it harder and harder to secure an apprenticeship under a master of the trade.
I fully support colleges and evening courses that offer classes on how to make a coat as it can really help a lot of people develop their skills and quench their thirst for knowledge. I myself enrolled in the London College of Fashions Handcraft Tailoring Diploma in 2005. The faculty made it out to be the only course one needed to take to become a tailor. That after one year you would know everything you needed to to venture into the trade and be a success. Of course, once I started there they sang a different tune. I was then told then that they don't turn out tailoring apprentices any more, the course was too short, the class sizes too big and the curriculum too broad to handle such a detailed subject as handcraft tailoring.
Our course on coat making was only one-third of the entire year, meaning we only had a few short months to get our project finished and learn all the skills necessary to do so. Since I had already learned coat making in Ireland, this reality was less daunting to me than many others in my class. I recalled being quite annoyed at the faculty for feeding me one story before I joined and another when l enrolled, l was hugely sceptical at their claims but wanted to believe them anyway. Even given my own experience, l would still encourage others to follow my footsteps and take a coat making class locally if one was available to you. Coat making is a highly skilled subject and even if you only got a brief introduction to it, with the support of the video series you would see it for what these courses really are. Just the first step in a long road to becoming a handcraft tailor.
I am not here to claim that my class on how to make a coat is the only resource you need to become a tailor. Any sort of tailoring experience you can get outside of my online coat making class will stand to you, even if it is only with a local alteration tailor. I myself worked with an alteration tailor for one year before emigrating to the UK. It was this experience that made me fall in love with tailoring again. l did learn some new skills, l improved my machine sewing techniques and l loved turning up to work every day to spend my time with a skilled and very experienced tailoring team who all just wanted to laugh and enjoy their workday.
If the video series is the only resource available to you, expect your road to be a longer one than someone who has had someone to one training. Don’t just jump in and try coat making straight away. Hone your skills first. Skip ahead to the pocket making and make some sample pockets to begin with. Check out the videos on hand sewing and take a sample piece of cloth to practise a basting stitch and the felling stitch. Become comfortable with your needle and thimble. You can’t become a handcraft tailor if you can’t use a thimble. Sewing without one is just passing a threaded needle through cloth.
Take your time and don’t rush it. We will be opening our doors again to in-house students when it is safe to do so. Get yourself going on the video series and if and when you can, sign up for some in-house lessons so we can focus on the areas you are weakest.
I suspect that students very soon will be bringing in their half-made garments so they can focus solely on the elements of coat making which has eluded them, such as collars or sleeve setting.
Since opening The Handcraft Tailor Academy in 2016, I have hosted in-house courses and then I started introducing online courses in 2017. I have helped scores of people realise their dreams of becoming garment makers. Unfortunately, the world is full of non-sewing “tailors” and too few really have the skills to claim any title.
The Making of a Savile Row Coat was produced for the aspiring tailor. Someone who couldn’t access the knowledge through the usual channels – for the college student who wanted to study tailoring but had to settle for fashion design or the apprentice who feels they are being held back and want to progress at a faster pace. Even other tailors who want to brush up on their skills or have difficulty with certain aspects of garment making and want to see how the pros do it.
Over the years, I have come to know many who wish to possess the knowledge of a Savile Row tailor but just lacked the opportunities until now.
The Making of a Savile Row Coat is a ’how-to’ video series that details the exact step by step process to make a handcraft coat. No detail is left out. These videos are painstakingly slow at times but that is to ensure the viewer is left in no doubt of every aspect of coat making.
Coats, being the most sought after garment to make, seemed like the best place to start when creating this video series but not necessarily the best place to start learning to become a tailor. Though our course on how to make a coat is quite comprehensive, coat making itself utilises a broader set of skills than either waistcoats or trousers. If coat making is your passion, then don’t let our words dissuade you. Our online and in-house coat making courses go hand in glove with one another. Even our in-house students use our coat making series as a guide when they also receive a live demonstration.
Each episode comes with a description so a student can skip ahead or pick up where they left off. There is no limit on how many videos you can watch or when – it’s full access for a monthly fee 24/7.
You don’t need fancy equipment to be a handcraft tailor. For much of the video series, I use a standard household iron for the under-pressing and final press off. A domestic sewing machine will sew a seam just as well as an industrial one.
But the one tool a tailor can’t do without is the thimble so I encourage you to take the time and learn that skill. Sleeve boards and chest boards (also known as a 'ham') is a must. New ones can be hard to come by and some haberdasheries do sell modern versions but old school ones are best. eBay is a great place to pick up old sleeve and chest boards and many Instagrammers are offering new ones for sale. In the future, I will add a post here on how to cut and make your own, as I do for my in-house students. Also, check out our forum for some online resources our community has shared.
That brings me to the trimming packages. I have partnered with Dugdale Brothers in Huddersfield, England. Dugdale’s are well known for being student-friendly, allowing tours of their establishment and even offering sponsorships.
We currently have three trimming packs available at trade (as opposed to retail) prices specifically for The HTA: the HTA coat, waistcoat and trouser pack.
These trimming packages contain everything and more to produce one garment. I use the same pack(s) in the video series so my materials will match with yours.
If you have any questions or comments please feel free to reach out. We would love to hear from you.
Best wishes,
Rory.
Comentarios